EDUCATIONAL-ATTESTATION WELDING CENTER
The training and certification center for the training of welders fully meets the modern requirements for the training process and represents a single set of the latest teaching and methodological and technical tools that allow specialists in electric arc welding and welding safety to be trained in a short time and with very high efficiency.
Welders training directions
This center allows you to carry out laboratory and practical classes in the following areas:
- Manual metal arc welding (MMA);
- Arc welding with a consumable electrode in shielding gases (MIG / MAG);
- Arc welding with non-consumable (tungsten) electrode in inert gases (TIG);
- The device and the principle of operation of welding equipment.
Technologies and equipment for underwater welding. Machine PH-161 "Neptun"
Unique technologies and equipment for underwater welding – allow work performance at any time of the year, in particular under the ice, at increased pressure and at other complicating factors. We guarantee a high quality and reliability of welds and joints of low-carbon and low-alloyed steels. Technologies and mechanization means for underwater welding processes were developed that is particularly important in emergency-rescue operations and operations under hazardous conditions. They allow an essential increase of welding operation efficiency, lowering of welding consumable and power consumption in view of optimization of the entire production process.
Technology for mechanized pulsed-arc consumable electrode welding with the pulsed mechanism for automatic feeding of welding wire. Machine PSh-007
For the first time in the world practice – the technology for mechanized and automated pulsed-arc consumable electrode welding, which features application of the pulsed mechanism for automatic feeding of welding wire synchronized with the operation of the pulsed source of welding current. Both the sources (pulsed current and pulsed feed of wire) are interconnected by automatic means – by an optimum algorithm of control of electrode metal drop transfer that allows an effective redistribution of melting energy of the electrode and base metal. Presented technology allows achieving in practice a considerable reduction of energy, labour and other resource consumption.
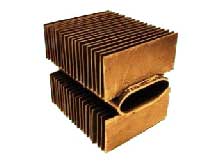
Fig. 1
The new power saving technology for improvoment of the efficiency of heat-exchange surfes of flat oval pipes
Innovation project developed together with NTUU “Kiev Polytechnic Institute” for the first time in the world practice – power-saving technology for improvement of the efficiency of heat-exchange surface of flat oval pipes with welded-on stiffeners (resistance welding). Flat oval pipes with incomplete finning of the surface (Fig.1) are applied in different industries (petroleum processing, chemical, gas, food industries, in gas transportation system, etc.) as heat-exchange carrier: water economizers, boiler unit heaters, boilers-utilizers, regenerators, oil coolers, dry cooling towers and air capacitors. Mastering new heat-exchange surfaces will lead to a considerable saving of metal (by approximately 1.5 – 2 times) and power resources, as well as lowering of the price for one running meter of pipes.
New generation automatic machine UD-682 is designed for welding plate bodies
New generation automatic machine UD-682 is designed for welding plate bodies by narrow-gap TIG with magnetic control of the arc (UD 682) and allows complete automation of electric arc welding process by a unique technology – by the method of automatic following of welding electrode position using a special device – arc sensor. Welding is performed by argon-arc process with tungsten electrode and filler wire, in several passes (number of which depends on welded item thickness). Components of leading foreign and local manufacturers are used in the machine. Automatic welding machine is applied in manufacture and repair of large-sized metal structures 20 – 110 mm thick.
New t echnology of highly efficient automated submerged-arc welding of vertical site butt
Innovation technology - of highly efficient and cost-effective automated submerged-arc welding is designed for welding vertical site butt joints of span structures of bridges and large metal structures with plate thickness from 12 up to 50 mm by solid wire under a layer of molten slag with compulsory formation of the seam to two copper shoes. The developed new welding process leads to a considerable saving of power, essential lowering of the cost of welding consumables and improvement of operating efficiency. This technology combines a quiet running of the process, characteristic of electroslag welding with the high quality of metal of the weld and HAZ (heat-affected zone), that is usually provided only by flux-cored expensive wire welding. In addition, the submerged-arc welding process is characterized by much lower emissions of welding aerosol compared to welding by self- shielded flux-cored wire and welder’s labour hygiene.
Technology and equipment for automated welding position circumferential butt joints of pipes ø426-1420 mm diameter, a wall of 7-26 mm. Machine AD-366T
Innovation technology and equipment-are designed for automated welding of position circumferential butt joints of pipes ø426-1420 mm diameter, a wall of 7-26 mm with standard plant V-shaped groove, by flux-cored wire with forced weld formation. The proposed technology is used in building and mounting of the main gas, oil and water pipelines on the line, especially in difficult-of-access places, where it is impossible to apply hoisting-transportation means and under the conditions of built-up areas of the route. Technology allows a significant improvement of labour efficiency through welding process automation, reducing non-productive losses, welding process labour content, improving welderlabour conditions, as well as saving power costs through optimization of the entire production cycle. Welding of pipe butt joints by this technology is performed by displacement of welding heads by a detachable mono-rail in the automatic mode around a stationary steel pipe of practically any diameter.
New generation of small-sized Machines series AD-333. The carriage AD-334
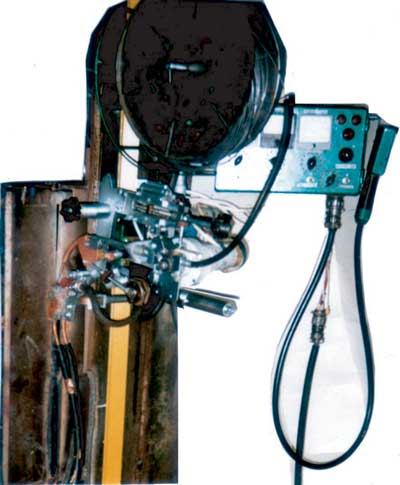
New generation of small-sized Machines series AD-333 (Fig.1) of various updatings are intended for arc welding with compulsory formation of a seam vertical, inclined, curvilinear, not rotary ring, and also horizontal joints (on vertical planes) of metal thickness of 8-60 mm at manufacturing, repair and installation sheet metal construction (Fig.2). Welding current - no more than 500 A, voltage of an arch 24-40V,electrode ø2-3 mm. The technology of welding is characterized by full absence of angular deformations and small cross-section contraction (up to 2 mm). The technology allows for one pass at one or to bilaterial welding to receive еqually strong with the basic metal welded connections. All machine of a series are supplied with devices for automatic maintenance of a level of a welding bath concerning the top edge of the forming device.
AUTOMATIC MACHINE FOR WET UNDERWATER WELDING IN CONFINED SPACES
PWI developed technology and equipment allowing performance of automatic flux-cored wire wet underwater welding of structural elements, reliably insulating the lower part of heat exchanger column. The unique aspect of the work consists in development of an automatic welding machine, capable of operating when immersed into a pipe of 119 mm inner diameter into liquid heat carrier medium at 200 m depth. The semiautomatic machine was designed with application of special torque electric drives for electrode wire feed and welding displacement mechanisms. A special cable with welding and control wires was developed, capable of operating at a large distance from the arc power sources and control system. Cable uncoiler design was also developed, with digital recording of automatic machine position along the pipe length. Approbation results showed that application of special automatic machine allows increasing heat exchanger reliability, reducing time loss during performance of work on its sealing, rational use of site area and reducing financial expenses. 5 Ref., 8 Figures.
The specialized assembly machine of new generation AD-381
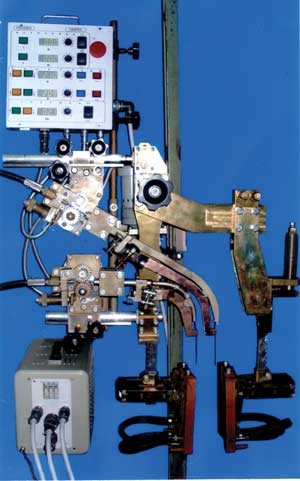
Fig. 1
The specialized assembly machine of new generation AD-381 (Fig.1) is intended for single-pass electroslag welding metal by thickness of 30-100 mm. The machine is supplied with two submitting mechanisms for wire ø2-4 mm with separate, independent regulation of speed of submission of each of them. Welding current 1000 A. The machine will consist of four modules quickly mounted with the help of a key without additional tools, that considerably reduces time at performance of the electroslag welding seam. As a directing rail used rolling steel angle by section 50x50 mm. The running carriage of maghine, moving on directing rail, besides performance of welding can serve as the running mechanism as for the cutting torch by preparation of joints under welding, and also for the machine providing the subsequent processing of welded connection.
Machins–arethe welding tractor ТС-77М, ТС-78М, ТС-79
Machins –arethe welding tractor ТС-77М, ТС-78М, ТС-79 are intended for automatic submerged-arc weldingbutting, angular, longitudinal and ring seams metal constructions thickness 10-50 mm in shipbuilding, at construction of bridges, tanks, etc., etc. The welding tractor ТС-78Мit is intended for automatic welding by two arches in slot-hole cutting for one pass of welded connections by thickness up to 50 mm.