Technologies and services required by industry- for manufacturing and mounting (welding-on) of heat-removing and load-lowering parts and structures: Nelson pins and "flexible" tie-bolts - are designed for mounting on metal structures exposed to high temperatures or high loads in service. Welding operations can be performed directly on objects under construction (bridges, overpasses, etc.) and on equipment in the Customer facility.
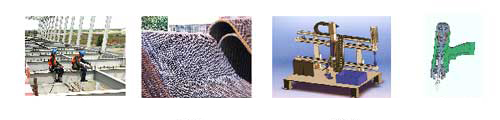
Applications:
- - nuclear-, hydro-, thermal power plants;
- - metallurgical, petroleum processing plants;
- - construction of residential and industrial facilities, trade centers (Fig. 1);
- - warehouses and logistic companies;
- - bridge construction and repair, including underwater sections;
- - gas- and oil pipelines;
- - working surfaces of rapidly wearing parts of equipment and machines, ladles, bulldozers, etc (Fig. 2).
Complex of means machanization welding processes
Application of means mechanization welding processes allows to raise productivity and quality of welding in all spatial positions, with application of various ways of protection. Offered welding machine allow to facilitate essentially work of the welder, is easily built in industrial technological lines. Welding current - no more than 360 A, electrode ø2-3 mm.
Welding automatic machineA-1698 (Fig.1) is intended for automatic electroarc welding angular seams by cathetus 4-8 mm in the bottom position in the environment of carbonic gas, with flux, with a speed 15-40 km/h and speed of submission wire 260-630 km/h. The automatic machine also is used for semi-automatic welding in the environment of carbonic gas.
Machine for welding taps of electric motors armature winding
Machine for welding taps of armature windings to commutator bars of drive electric motors instead of brazing – provides a considerable cost effect (in production and repair) due to saving of expensive braze alloys, thus essentially extending the electric motor service life. Welding of taps of armature windings is performed by a nonconsumable electrode in a shielding gas atmosphere, mostly of helium or mixtures on its basis (TIG welding).
Technologies of hardfacing the wear surfaces by flux-cored strip and wire
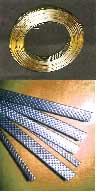
Technologies of improvement of the reliability and fatigue life of equipment by the method of hardfacing the wear surfaces by flux-cored strip and wire alloys are designed for protection of metal structure surfaces under the conditions of abrasive wear in reactive media, exposure to increased temperature, contact-shock loading, hydroabrasive, cavitation and gas-abrasive wear. Flux-cored welding consumables guarantee an unprecedented corrosion resistance of the treated surface, considerable increase of their wear resistance, extension of facilities service life, considerable saving of labour resources and circulating assets in repair-reconditioning operations and service, as well as high labour efficiency at welding process automation.
Modern automated control systems
Modern automated control systems- are designed for welding equipment control. High level of control systems is achieved due to application of ingenious engineering solutions and advanced electronic components (programmable logic controllers, variable-frequency drives, sensor terminals, sensors and controls) from leading world manufacturers (Omron, Siemens, etc.). Technological process monitoring and control of equipment operation are performed by systems of visualization and parameter recording.